Understanding Your CNC Tevo Tarantula
The Tevo Tarantula CNC is a popular choice for hobbyists and makers looking to delve into the world of computer numerical control machining. It’s a versatile machine capable of cutting, engraving, and shaping various materials, from wood and plastics to softer metals. Understanding the fundamental components and their functions is the first step towards mastering this exciting technology. This guide will provide you with the necessary information to get started and optimize your CNC Tevo Tarantula for success.
Essential Components
A CNC machine, like the Tevo Tarantula, comprises several key components working in concert. These components, when properly assembled and calibrated, enable precise and repeatable movements. Familiarizing yourself with these parts is crucial for troubleshooting and optimizing performance.
Frame and Build Plate
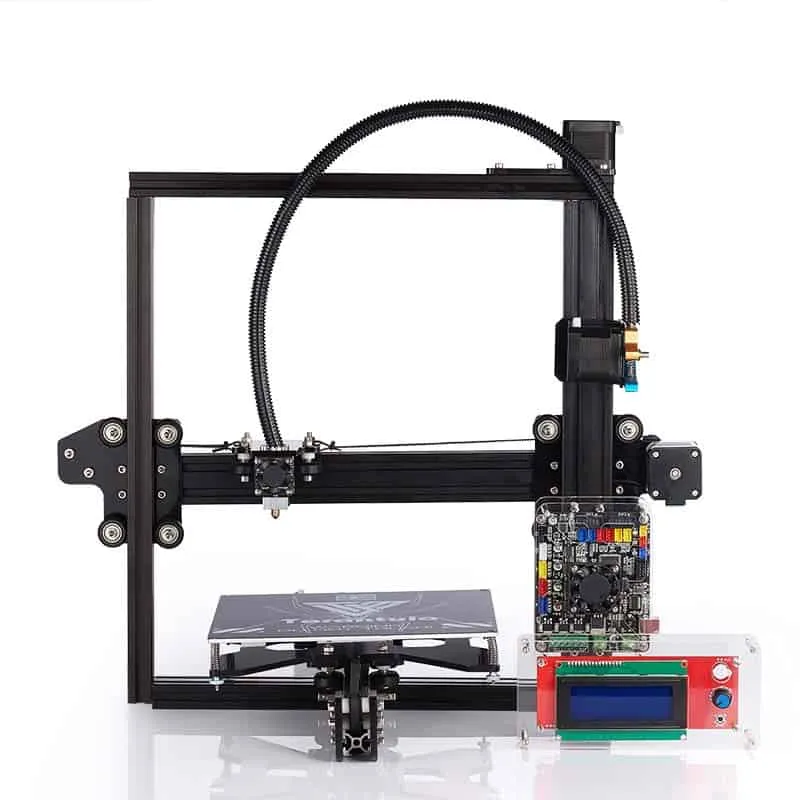
The frame provides the structural support for the entire machine. It must be rigid and stable to minimize vibrations during cutting. The build plate, or work surface, is where you mount your material. Ensuring the build plate is level and securely mounted is essential for accurate cuts. Many Tevo Tarantula owners upgrade the build plate for improved flatness and durability. Proper frame assembly and build plate preparation are therefore critical for initial setup and subsequent use of the machine. This helps maintain precision during operation.
Stepper Motors and Drivers
Stepper motors are responsible for precise movement along the X, Y, and Z axes. They are controlled by stepper motor drivers, which translate digital signals from the control board into the motor’s electrical pulses. The quality of the stepper motors and drivers affects the accuracy and smoothness of the cuts. Upgrading these components can significantly improve the performance of your CNC Tevo Tarantula, allowing for finer detail and faster cutting speeds. Always ensure your drivers are appropriately configured to match your stepper motors for optimal performance.
Control Board
The control board is the brain of the CNC machine, receiving instructions from the computer and controlling the movements of the stepper motors. It interprets the G-code (the language of CNC machines) and sends signals to the drivers to move the motors. The control board also manages other functions, such as spindle speed control and end-stop sensors. Common control boards for the Tevo Tarantula include those based on the Arduino platform. Selecting a board that supports your desired features and cutting speeds is a critical consideration when setting up your machine.
5 Pro Tips for CNC Tevo Tarantula Success
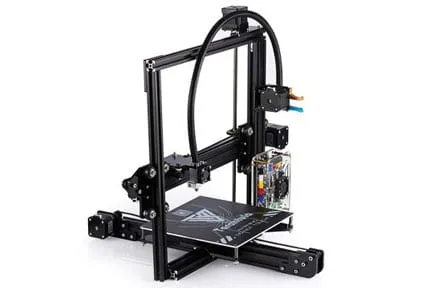
Getting the most out of your CNC Tevo Tarantula requires more than just assembling the machine. These five pro tips will help you improve your results, avoid common mistakes, and enhance the overall user experience. Applying these practical techniques helps achieve higher-quality results and increased machine longevity.
Tip 1 Leveling the Bed Perfectly
Bed leveling is arguably the most crucial aspect of CNC operation. An uneven bed will result in inconsistent cutting depths, poor quality, and potential damage to the machine or the workpiece. Spending time on bed leveling is an investment that pays off in the long run with improved precision and fewer errors.
Why Bed Leveling is Crucial
The CNC bit needs to be at the correct height relative to the material to achieve the desired cuts. If the bed is not level, the bit will cut deeper in some areas and shallower in others. This leads to inconsistent results, including incomplete cuts, excessive material removal, and even broken bits. Moreover, if the bed is significantly unlevel, you risk damaging the CNC bit, the build plate, or even the machine itself. Perfect bed leveling guarantees a uniform and consistent cutting depth across the entire surface of your material.
Methods for Bed Leveling
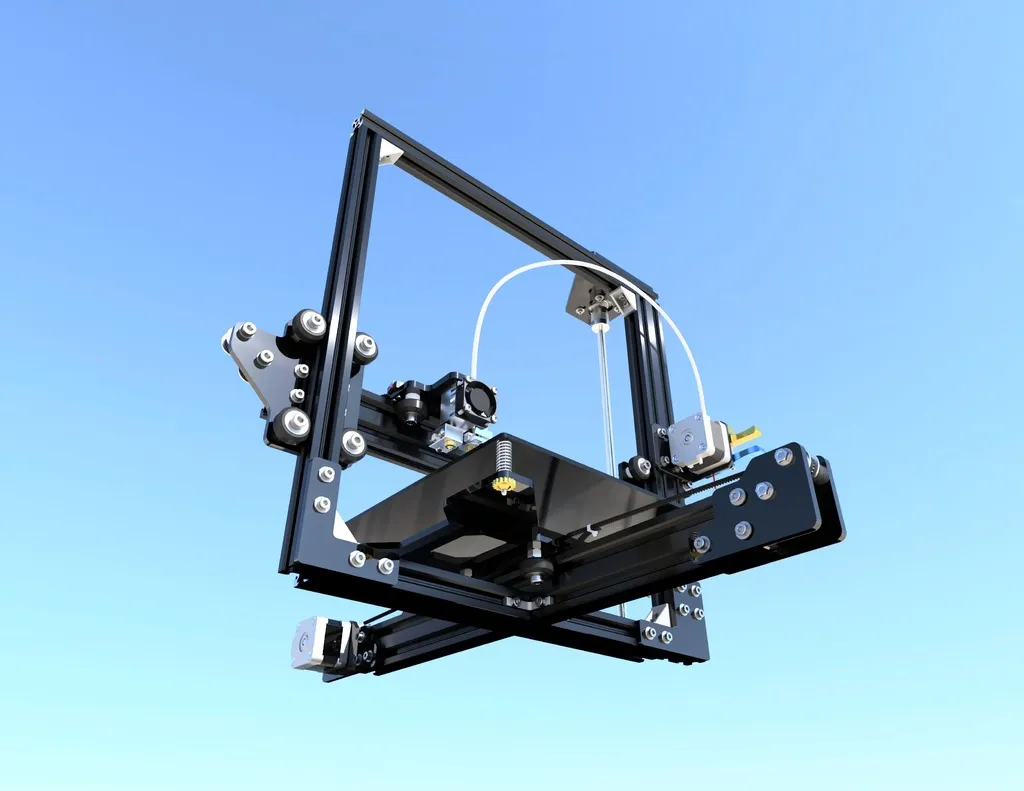
There are several methods for leveling your CNC bed, each with its advantages. Manual leveling typically involves adjusting screws at each corner of the bed while using a level or feeler gauges to ensure the surface is flat. Another method involves using auto-leveling sensors, which measure the distance between the bit and the bed at multiple points. These sensors automatically compensate for any imperfections in the bed’s surface. Regardless of the method used, the key is to ensure the bed is as level as possible before each cutting session. Regular calibration and adjustment are often required to maintain accuracy.
Tip 2 Choosing the Right CNC Bit
Selecting the appropriate CNC bit is critical for achieving the desired results and maximizing the lifespan of both the bit and your CNC machine. Different bits are designed for specific materials and cutting operations. Choosing the wrong bit can lead to poor cuts, excessive wear, and potential damage. Bit selection involves considering the material, the desired cut type, and the finish required.
Types of CNC Bits and Their Uses
There’s a wide variety of CNC bits available, each with its unique characteristics and intended uses. End mills are versatile bits used for a variety of cutting operations, including profiling and pocketing. Ball nose bits are suitable for creating rounded edges and 3D carvings. V-bits are ideal for engraving and detailed work, especially in wood. The choice of bit depends on the project and the material being cut. Understanding the strengths and weaknesses of each bit type enables you to select the best tool for the job.
Material Compatibility with Bits
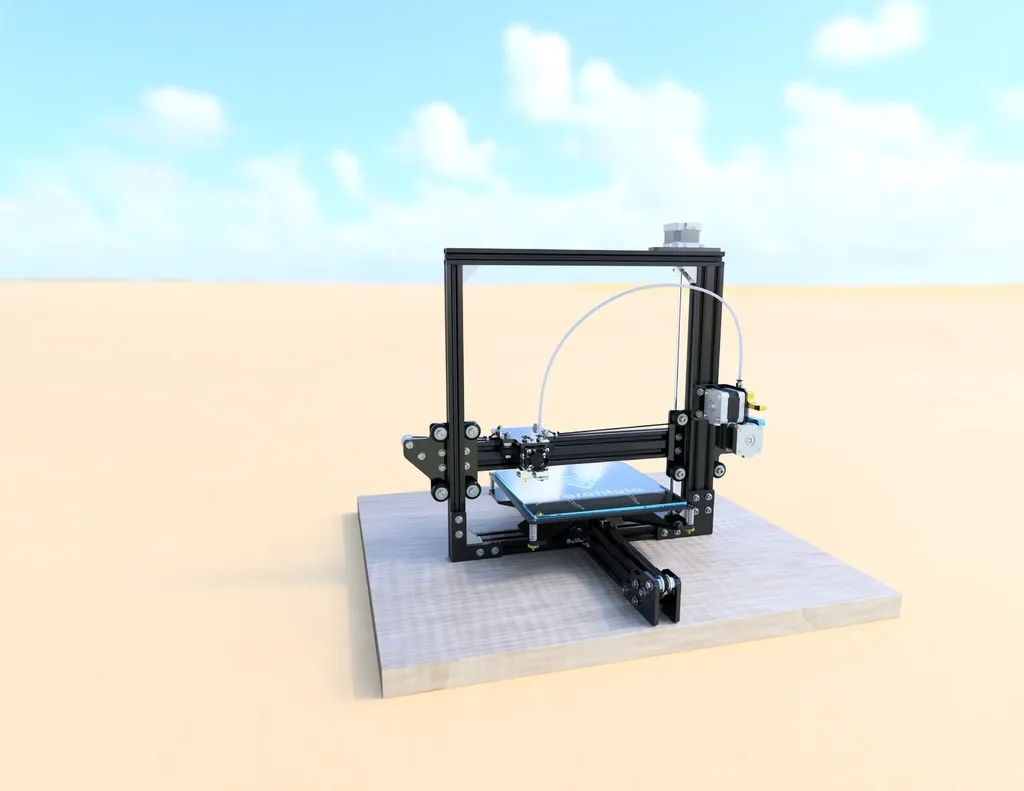
Not all bits are suitable for all materials. Some bits are designed for use with wood, while others are better suited for plastics or metals. Using the wrong bit can cause the bit to break, dull quickly, or produce poor-quality cuts. Consider the material’s hardness, density, and melting point when selecting a bit. For example, carbide bits are generally more durable and can handle harder materials than high-speed steel bits. Researching the appropriate bit for the material you intend to cut will save time and money and ensure you get the desired results.
Tip 3 Mastering the Software
CNC machines are controlled by software that translates designs into instructions for the machine. Learning to use the software effectively is vital for creating successful projects. Understanding the interface, the G-code, and the various settings will enable you to design and execute complex cuts. The software serves as the bridge between your creative vision and the physical outcome of the CNC machine.
Popular CNC Software Options
Several software options are available for CNC machines, each with its features and capabilities. Some popular choices include Fusion 360, Easel, and VCarve Pro. Fusion 360 is a powerful, cloud-based CAD/CAM software suitable for complex designs and advanced users. Easel is a user-friendly option for beginners, ideal for simple projects and learning the basics. VCarve Pro is a professional-grade software that offers advanced features for creating intricate designs. The choice of software depends on your experience level, the complexity of your projects, and your budget. Researching and experimenting with different software programs is essential to discover what works best for your needs.
G-Code Basics
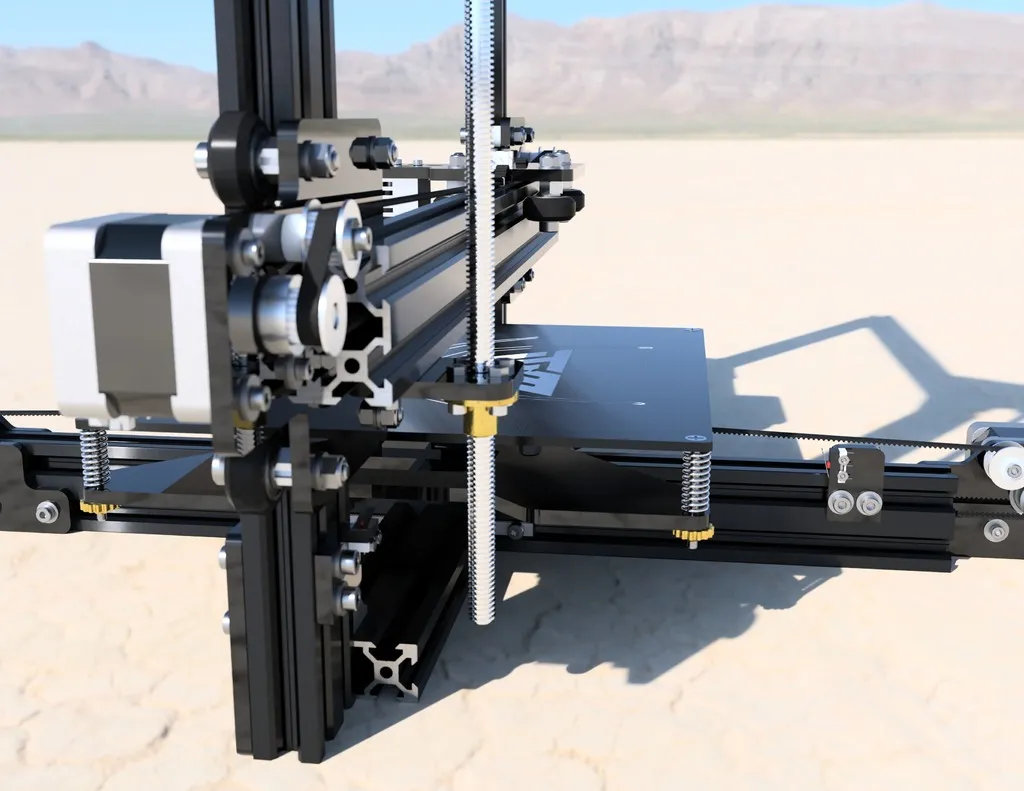
G-code is the programming language that instructs the CNC machine on how to move. It comprises a series of commands that control the movement of the bit, the spindle speed, and other machine functions. Understanding G-code is useful for troubleshooting and making minor adjustments to your designs. While you do not need to become an expert in G-code to use your CNC machine, familiarity with its basics will give you greater control and allow you to optimize your cutting processes. Learning the meanings of key G-code commands allows users to create and edit toolpaths for very specific results.
Tip 4 Optimizing Your Cutting Parameters
Setting the correct cutting parameters, such as feed rate, spindle speed, and depth of cut, is crucial for achieving high-quality cuts and preventing damage to the machine or the workpiece. Incorrect settings can lead to poor surface finishes, broken bits, and even machine failures. Experimenting with different settings and understanding their impact on the cutting process is essential for achieving optimal results. Proper parameter selection reduces both material waste and cutting time.
Feed Rate and Spindle Speed
The feed rate is the speed at which the bit moves through the material, while the spindle speed is the rotational speed of the bit. The optimal settings for these parameters depend on the material being cut, the type of bit used, and the desired cut quality. Generally, harder materials require lower feed rates and higher spindle speeds. The appropriate balance between these two parameters ensures efficient cutting and minimizes wear on the bit. Experimentation is key to finding the best combination for your specific projects. Incorrect settings cause burns, chipping, or even machine stalls.
Depth of Cut
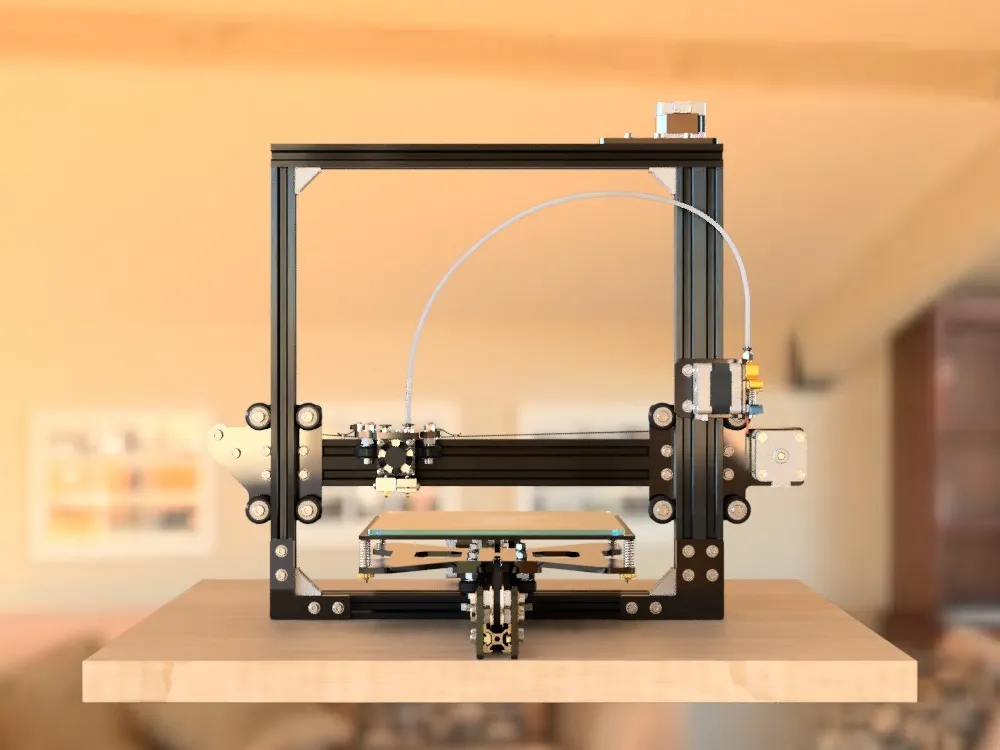
The depth of cut is the amount of material removed by the bit in each pass. Taking multiple shallow passes is usually preferable to a single deep pass, especially when cutting hard materials. This reduces stress on the bit and the machine and improves the accuracy of the cut. The optimal depth of cut depends on the material, the bit being used, and the desired finish. Always consult recommended cutting parameters for your chosen material and bit before starting a project. Too deep a cut can result in the bit breaking or the machine stalling.
Tip 5 Safety First
CNC machines involve moving parts and can generate dust and debris, making safety a top priority. Following safety guidelines helps prevent injuries and ensures the longevity of your machine. Always prioritize safety, as it is essential for a positive and productive CNC experience.
Personal Protective Equipment (PPE)
Wearing the correct PPE is essential when operating a CNC machine. This includes safety glasses to protect your eyes from flying debris, a dust mask or respirator to prevent inhaling fine particles, and hearing protection to reduce noise levels. Gloves can also be helpful when handling materials and bits. Make sure your workspace is well-ventilated to remove dust and fumes. Safety is not optional; it’s a requirement for all users. A dedicated workspace setup with safety gear is the first step in operating a CNC machine safely.
Workspace Setup
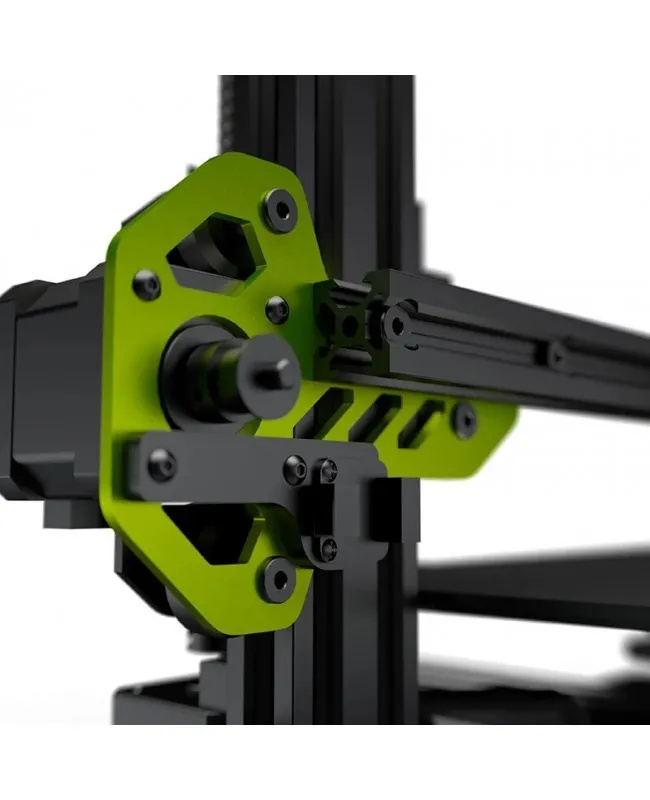
Your workspace should be clean, well-lit, and free of obstructions. Make sure the machine is placed on a stable surface, and that there is enough space around it for you to move safely. Consider setting up a dust collection system to remove dust and debris. Keep flammable materials away from the machine and never leave the machine unattended while it is running. Regular cleaning and maintenance of the workspace will enhance safety and maintain the machine’s longevity. Always follow safety guidelines provided by the manufacturer.
Troubleshooting Common Problems
Even with careful setup and operation, you may encounter issues with your CNC Tevo Tarantula. Understanding the common problems and their solutions can help you diagnose and resolve issues quickly and efficiently. These are often the result of improper settings, machine wear, or software glitches.
Printing Errors and Solutions
Printing errors can manifest in various ways, such as incomplete cuts, rough surfaces, or misaligned features. Common causes include incorrect cutting parameters, a loose bit, or a problem with the G-code. Always review your G-code to ensure it’s correct and that the toolpaths are appropriate for your material. Check the bit to ensure it is securely fastened and is the correct type. Adjust feed rates, spindle speeds, and depth of cut to optimize the cutting process. If the issues persist, consult online forums or the machine’s manual for additional troubleshooting steps.
Calibration Issues
Calibration problems, such as incorrect dimensions or misaligned axes, can be frustrating. Issues with calibration can often be traced to improper belt tension or issues with the stepper motor drivers. Refer to your machine’s manual to understand the calibration process and follow the instructions carefully. Verify that the belts are properly tensioned and that the axes are aligned correctly. Sometimes, calibration issues arise from loose screws or from the build plate. Regularly calibrate your machine, especially after making adjustments or after prolonged use. Regularly maintaining the equipment will minimize issues.
Maintenance and Upgrades
Regular maintenance is crucial for keeping your CNC Tevo Tarantula in top condition and extending its lifespan. This includes cleaning the machine after each use, lubricating moving parts, and checking for loose screws or other potential issues. Performing routine maintenance and considering upgrades will increase the performance and longevity of your CNC machine. Regular maintenance prevents long-term issues and enhances the overall user experience.
Upgrade components to enhance your machine’s performance. Consider upgrading the control board, stepper motors, or build plate for better accuracy and capabilities. Researching and implementing upgrades is a great way to maximize your machine’s potential. Properly maintaining your Tevo Tarantula CNC machine ensures consistent, high-quality results for years to come.